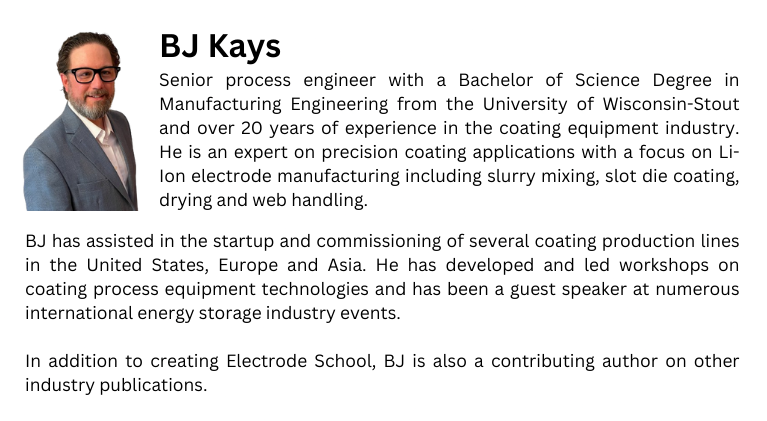
Chapter 3: Slurry Preparation
Authors: W. Blake Hawley, William Kays, and Jianlin Li
Publication: Processing and Manufacturing of Electrodes for Lithium-Ion Batteries
https://doi.org/10.1049/PBPO227E_ch3
Abstract
As will be detailed throughout this book, the state-of-the-art lithium-ion battery (LIB) electrode manufacturing process consists of several interconnected steps. There are quality control checks strategically placed that correlate material properties during or after a particular step that provide details on the processability (i.e., compatibility with downstream manufacturing processes) and, sometimes, projected performance of the finished product. In this chapter, we will begin this exploration by starting with the first step in the state-of-the-art LIB process, which is preparation of the electrode slurry. Alternative terms to "slurry," such as ink, paste, or (less commonly) dispersion, are sometimes used in academia or industry.
Chapter 4: Slot Die Coating
Authors: William Kays, W. Blake Hawley, and Jianlin Li
Publication: Processing and Manufacturing of Electrodes for Lithium-Ion Batteries
https://doi.org/10.1049/PBPO227E_ch4
Abstract
Continuing with the concepts discussed in this text the next interconnected step in the lithium-ion battery (LIB) manufacturing process is electrode slurry application onto the metal foil current collector. This process is commonly referred to as a coating process; however, in practice, the current methods are founded and fundamentally very similar to legacy processes used in the printing, photographic film, and magnetic media industries. Those industries have all seen a decline in market demand over the last few decades while the market demand for LIB has and continues to increase. The state-of-the-art coating process has been and continues to be slot die coating, employing a variety of configurations depending on a host of process variables such as target electrode loading mg/cm2, foil current collector thickness and quality, production plant layout, target coating width, and production machine speed range which is commonly referred to as the coating line speed or simply line speed.
Chapter 8: Electrode Drying and Calendering
Authors: W. Blake Hawley, William Kays, and Jianlin Li
Publication: Processing and Manufacturing of Electrodes for Lithium-Ion Batteries
https://doi.org/10.1049/PBPO227E_ch8
Abstract
Once the lithium-ion battery (LIB) electrode slurry is applied to the current collector, the solvent from the coating must be removed in the drying step. Occasionally, the qualifier "primary" is used to differentiate this step from downstream secondary drying, which is used to reduce the moisture content of electrodes. Electrode drying most commonly occurs in long convection ovens that are placed in-line with the coating apparatus. In other words, the current collector starts as a bare foil, then is coated, and fed into the drying oven all in one step without any need for switching the foil onto a new roll. Knowing the speed of the substrate, the dryer can be sized appropriately to secure that there will be sufficient time for the solvent to be removed. The synergy between coating and drying is beneficial for process efficiency but requires a high degree of tuning and quality assurance to ensure that the electrodes are being dried well.
After the electrode is dried, it is passed to a machine that reduces the thickness of the electrode. The machine, commonly called a calender and sometimes called a rolling press, consists of two rollers that are rotated in opposite directions (i.e., one clockwise and the other counterclockwise). A gap is set between the rollers that can be correlated to the desired thickness of the electrode. Since energy density is essential for LIB electrodes in many applications, calendering is a useful process for reducing excessive void space in the electrodes that contribute nothing to energy density. However, the balance between thickness/porosity and electron/ion transport, as well as the effect on electrode mechanical properties, must be considered carefully when determining the optimal calendering conditions.
Further downstream in manufacturing, typically right before the electrodes are built into a cell, a secondary drying step is often employed. This secondary drying step is necessary to keep the moisture content of the electrodes low since moisture can harm the performance and safety characteristics of the cell. However, the secondary drying step time should be minimized to avoid process bottlenecks and excessive manufacturing energy costs.
In this chapter, these three processes will be discussed. The effect of each process on the electrode microstructure and resulting electrode performance is considered, as are the characterization methods of electrodes after each stage.